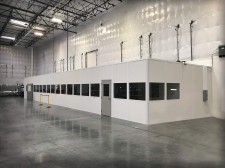
ATLANTA, June 5, 2019 (Newswire.com) - "Going Green" and protecting the environment is a movement that has become more and more important to companies, organizations, and countries across the globe. And these groups look to implement green standards and practices in every application they possibly can; all moving towards a common goal of living and operating in a sustainable and ecologically friendly world. The main targets of these movements include areas such as transportation, energy/fuels, agriculture, water conservation, and even construction.
Modular Building, by nature, is material and resource efficient.
The construction industry is often focused on due to the considerable amount of waste it generates, and according to Construction & Demolition Recycling, the "global volume of construction debris to nearly double by 2025," resulting in 2.2 Billion tons of waste each year. Industry leaders are looking to find any way possible to minimize this number. Luckily, as more and more industry experts have seen, modular construction can help with this issue.
Minimizing Material Waste
Perhaps the biggest benefit modular construction provides the "Going Green" movement is its ability to reduce the overall amount of material waste that results from a construction project. According to McGraw Hill Construction's SmartMarket Report, "Prefabrication and Modularization: Increasing Productivity in the Construction Industry," 76% of current modular construction users saw a decrease in the total amount of waste at their construction site. And 41% saw a decrease in waste of 5% or more. In terms of the construction waste forecast for 2025, a reduction of 5% would save 110,000,000 TONS of waste in that year alone.
So, why does modular construction do a better job of controlling their material waste? Well, there are a number of factors at play.
Controlling the Construction Environment
Modular construction facilities function much closer to a factory-style manufacturing facility than an actual construction site. Assembled structures in an assembly line like work progression. This is a closed, very controlled system that can closely follow materials through each stage in the manufacturing process.
In contrast, a construction site will typically have a stockpile of materials sitting around on site, waiting to be used. This can be a problem for two reasons…
First, on-site construction materials are susceptible to weather damage. For example, let's say a construction site is put through a particularly bad thunderstorm. If the materials are not properly protected, they can sustain severe water damage which will render them unusable for the project. Or in a potentially worse scenario, the materials can be picked up and thrown due to high winds, not only will the materials, in this case, be damaged, but this could result in damage to surrounding people or properties.
In a modular construction environment, there is no risk of damage to materials due to adverse weather. If modular structures are shipping in bad weather, the buildings will already be packaged and shrink wrapped so it's weather sealed for delivery.
Second, stockpiled goods at a construction site can be susceptible to burglary and theft. Depending on the materials used at the job site, they could be an attractive target for thieves. If a construction site does not have a solid security team, these materials can be taken, which makes them as good as wasted as far as construction companies are concerned.
A modular construction facility, of course, is an enclosed inside a factory environment that is fully locked and secured after hours. Therefore, these companies do not have the same theft risks as a semi-open construction site.
Accounting For Materials
Similarly, modular construction facilities have tighter control and over site of their materials. At a modular construction facility, each piece of material has a predetermined space for it to be kept as inventory. Inventory is easily supervised and followed from each process in the manufacturing process. On a job to job basis, someone might not be able to observe the benefit of having this tight inventory control. However, when a modular construction facility has over a thousand individual jobs over the course of a single year, it helps reduce spillage.
Over the course of many modular construction projects, or say one gigantic construction project that can last over a year long, there are many opportunities for materials to go by the wayside. They don't have to be ruined or stolen. The materials can just simply be lost, misplaced, forgotten, or contain a defect. All of these things can result in waste and lessens the overall production volume that would otherwise be obtainable. This spillage can also lead to increased scrap materials, production delays, and worst of all, a waste of valuable time.
Flexibility for The Future
Modular structures offer is flexibility for the future. With modular offices and mezzanines being a semi-permanent structure, they have the ability to be disassembled and reassembled in a new location.
This is a big factor especially when looking at it in reference to stick-built construction. One of the biggest contributing factors to the waste produced by the construction industry is the materials discarded after the structures are to be taken down. For stick-built, it is very difficult to reuse these materials and generally, they will find their way into a landfill, never to be used again.
However, looking at one of the modular office systems, for instance, a panelized wall system can easily be uninstalled, piece by piece. From there, the materials can be transported to a new location and reinstalled, ensuring the panels stay in use. Additionally, the offices can be reconfigured by adding more wall panels to them. This is a great technique to use for rapidly growing companies that need office space now and will likely need to expand even further in the future.
The pre-assembled buildings are erected atop a forkliftable steel base. Whether the building is a simple 4'x4′ guard shack or even an 8'x20′, the building can be moved from place to place depending on the facility's needs.
Integration of Other Green Products Like LED Lighting
In addition to being a Green Way to Build, modular structures also integrate a number of green products so that our buildings may operate greenly too. One major change Panel Built has made over the years is the commitment to using LED lighting as often as possible in all of our modular projects.
How Do LEDs Help Buildings Go Green?
LED lights provide a number of benefits over the industry's standard fluorescent light bulb. The biggest benefit to customers have seen is the incredible boost in lifespan they can expect from LED lights. On average, a fluorescent light bulb will have a typical lifespan of around 7,000 to 15,000 hours. However, an LED light can last anywhere from 50,000 to 100,000 hours! That increase in lifespan means less florescent bulbs going into a landfill (up to 14 fluorescent bulbs over the lifetime of an LED).
Also, the LED lights are much more durable than their fluorescent counterparts. Through a modular construction project, there is a lot of transportation of materials. No matter how carefully each fluorescent bulb is handled they are still incredibly fragile and highly susceptible to breaking. And when they do break, they instantly create hazards at the job site in the form of broken glass and toxic gases like mercury! LEDs solve both of these problems, reducing waste and hazardous materials.
Finally, when in operation LEDs are more energy efficient than fluorescent bulbs. When LEDs give off light there is much less wasted energy in the form of radiation. Fluorescents use phosphor which glows when it comes in contact with UV radiation, creating light and heat (15% of this energy is lost through heat and energy dissipation). LEDs operate using a semiconductor material which gives off light. For this reason, when a LED is on and operating it will give off little to no excess heat.
Source: Panel Built
Share: